2015 verabschiedete das Europäische Parlament eine wegweisende Richtlinie für den Umweltschutz. Das Ziel: den Verbrauch von leichten Plastiktüten bis 2025 um stolze 80 Prozent zu reduzieren. Unter diese Definition fallen Tüten mit einer Wandstärke von bis zu 50 Mikrometern – dazu zählen auch die bekannten Plastik-Einkaufstaschen in Supermärkten.
Um dieses Ziel in Deutschland erreichen zu können, setzten sich die Politiker mit dem Handel an einen Tisch – mit nachhaltigem Erfolg: In einer freiwilligen Vereinbarung sagten die Unternehmen zu, ab Juli 2016 Plastiktüten nur noch gegen eine Gebühr anzubieten. Manche schafften die umweltbelastenden Tragetaschen in diesem Zuge auch ganz ab. Ein historischer Schritt auf dem Weg zur erdölfreien Plastikproduktion. Trotz des Trends zu grünen Alternativen nähert sich das Kapitel Plastik aber noch lange nicht seinem Ende. Aber wo anfangen?
Biokunststoff: umweltfreundlich, aber in Konkurrenz zur klassischen Plastikindustrie
Außer der Alternative Papiertüte gibt es einen vielversprechenden Weg, um den Verbrauch von fossilen Rohstoffen zu senken: Grünes Plastik aus nachwachsenden Rohstoffen. Eines der attraktivsten Vertreter dieser Bio-Polymere ist Polylactid, kurz PLA. PLA besteht nicht nur zu 100 Prozent aus biologisch abbaubaren Materialien — es kann dank seiner physikalischen und mechanischen Eigenschaften herkömmliche, erdölbasierte Polymere in vielen Bereichen ersetzen. Und damit die weltweite CO2-Bilanz nachhaltig verbessern. Als Ausgangsstoff für die PLA-Produktion dient Milchsäure, die aus nachwachsenden Rohstoffen wie Zucker, Stärke oder Cellulose gewonnen wird.
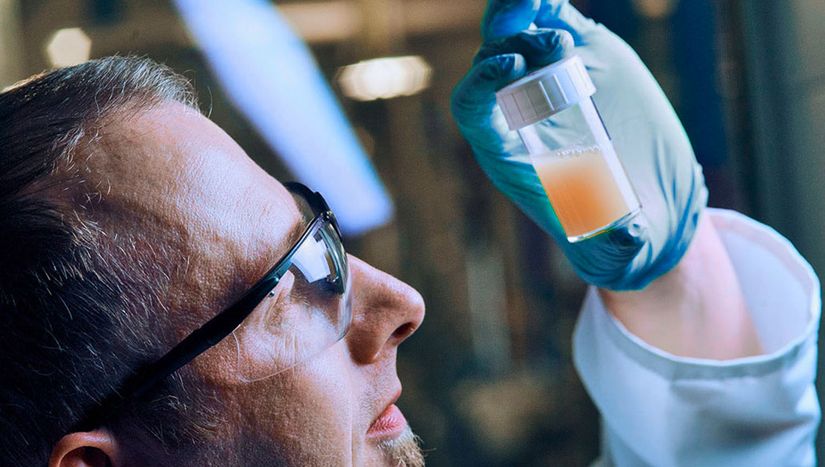
Eine Konkurrenz zur Nahrungsmittelproduktion ist PLA nicht – im Gegenteil, erklärt Udo Mühlbauer von thyssenkrupp, der Experte für den Biokunststoff ist.
Zum einen ist der Flächenbedarf für den Anbau der benötigten Rohstoffe extrem gering. Zum anderen besteht das Potenzial, Abfälle aus der Lebensmittelindustrie für die Herstellung von PLA wiederzuverwenden.
Competing with the classic plastics industry
PLA zum wirtschaftlichen Durchbruch zu verhelfen ist jedoch alles andere als einfach. „Biokunststoffe wie Polylactide stellen sich gegen den etablierten Kunststoffmarkt. Erdölbasierte Polymere werden in riesigen Anlagen produziert und können so deutlich günstiger hergestellt werden. Der Markt für Biokunststoffe ist im Vergleich dazu sehr klein und die Produkte damit teurer“, weiß Experte Mühlbauer. Während die Eigenschaften klassischer Kunststoffe zudem jahrzehntelang für verschiedene Anwendungsbereiche angepasst worden sind, stehen Biokunststoffe aktuell noch am Anfang ihrer Entwicklung.
PLAneo®:thyssenkrupp macht Polylactid zur echten Alternative
thyssenkrupp ist diese Herausforderungen angegangen – und hat in den vergangenen Jahren ein eigenes Herstellungsverfahren für den Biokunststoff entwickelt. Im chinesischen Changchun setzen wir eine patentierte Technologie namens PLAneo® seit kurzem zum ersten Mal bei einer kommerziellen Anlage ein. Unser Kunde: die Jilin COFCO Biomaterial Corporation, eine Tochter von Chinas größtem Lebensmittel- und Getränkekonzern.
Der große Vorteil von PLAneo®: Die Technologie macht es möglich, den Biokunststoff besonders effizient und ressourcenschonend zu produzieren – und das zu einem Preis, der mit herkömmlichem Plastik konkurrieren kann. Hierbei profitierte thyssenkrupp vom jahrzehntelangen Know-how aus dem Bau von mehr als 400 Kunststoffanlagen weltweit. „PLAneo eignet sich auch für großtechnische Anlagen mit Kapazitäten von bis zu 100.000 Tonnen pro Jahr. Das senkt die Produktionskosten entscheidend“, so Udo Mühlbauer, der die chinesische Anlage eng betreut. „Außerdem haben wir den Energieverbrauch des Verfahrens durch ein Energierückgewinnungssystem reduziert. Auf diese Weise senken wir die Kosten weiter und machen die Produktion gleichzeitig nachhaltiger.“
PLAneo eignet sich auch für großtechnische Anlagen mit Kapazitäten von bis zu 100.000 Tonnen pro Jahr. Das senkt die Produktionskosten entscheidend.
Udo Mühlbauer,
thyssenkrupp
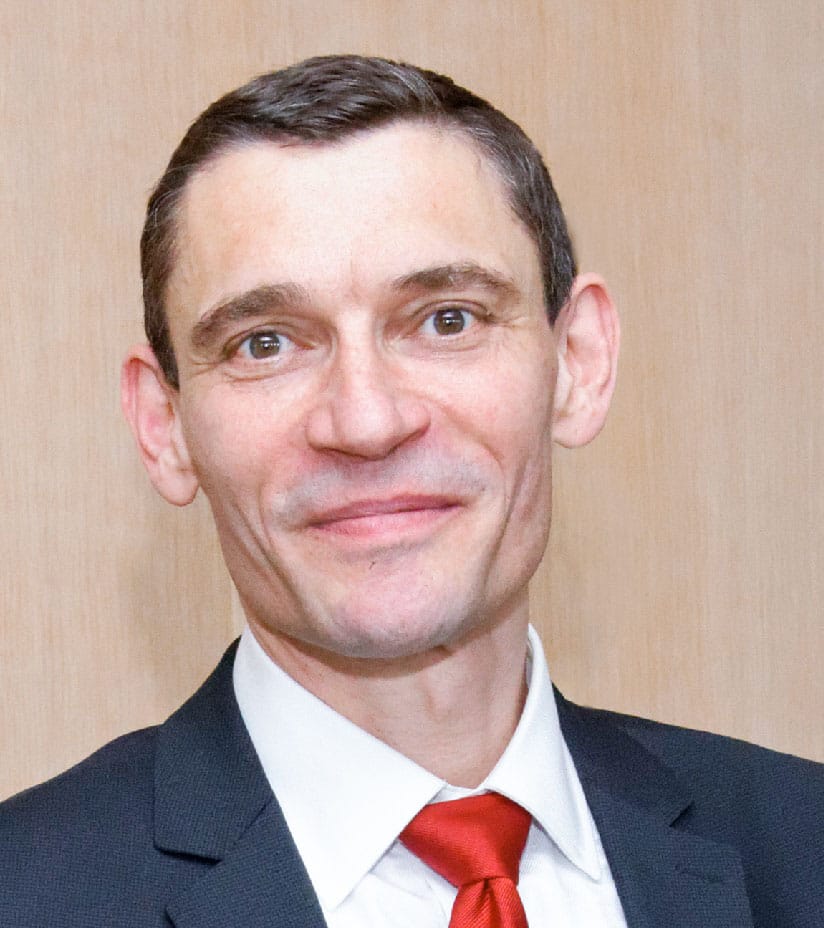
PLA ist für fast alle Anwendungsgebiete gewappnet
Denn PLA ist hochflexibel einsetzbar: vom Kosmetiktiegel, Sparschwein und Luftpolster über Besteck, Kulis und Sitzunterflächen für Bürostühle – vor erdölbasiertem Plastik muss es sich auf keinem Gebiet verstecken. Vor allem nicht im Medizinbereich, weil der menschliche Körper PLA restlos abbauen kann. Damit eignet es sich perfekt für Implantate, Nahtmaterial, Stents oder als Basis für die Züchtung von Gewebe.
Auch in der Landwirtschaft sieht Udo Mühlbauer viel Potenzial für den Einsatz des grünen Kunststoffs: „Mulchfolien aus herkömmlichem Plastik sind insbesondere in China ein großes Problem: Oft lassen die Landwirte die alten Folien auf dem Acker, sodass sie vom Wind verweht oder in die Äcker eingepflügt werden – dadurch sinkt die Bodenqualität. Biokunststoffe, insbesondere eine Kombination aus Polyester und PLA, können problemlos eingepflügt werden, denn sie verrotten mit der Zeit.“ Für industrielle 3D-Druckverfahren ist PLA ebenso geeignet. Und mit kompostierbaren Bio-Müllbeuteln und Kaffeekapseln aus PLA kann jeder den eigenen Haushalt Schritt für Schritt nachhaltiger gestalten.
Die Zukunft von Biokunststoff: große Herausforderungen – tolle Perspektiven
Klar ist aber auch: Der Weg zur erdölfreien Plastikproduktion ist noch weit. Auch, weil PLA teilweise keinen guten Ruf besitzt – entgegen seines Potenzials. So könnten biologische Abfallstoffe genutzt werden, um die benötigten Flächen für nachwachsende Ausgangsmaterialien zu minimieren. Und auch die Abfallsysteme müssen sich auf die umweltfreundlichen Materialien umstellen, denn noch gibt es selbst in Deutschland keinen eigenen Recycling-Pfad für PLA-Produkte – die wertvollen Rohstoffe werden deshalb oft mit dem herkömmlichen Plastikmüll verbrannt. Und auch die weltweiten Lieferketten sind noch nicht ressourcenschonend genug.