Green ammonia is no longer a pipedream. What’s more, since ammonia is a high-density energy carrier, it is also suitable for offsetting the fluctuations in the availability of renewable energy sources. Traditionally, ammonia production has been based on natural gas or coal and thanks to optimized technology the economies of scale for plants producing more than 3,000 metric tons/day (mtpd) make this process very cost-competitive. However, as these plants also emit high levels of greenhouse gases, thyssenkrupp developed an ammonia production concept that is moving towards more climate-friendly feedstocks than fossil fuels. Besides climate considerations, other drivers of the move to distributed production of “green” ammonia from small-scale plants have been the desire for localized self-sufficiency, avoidance of high transportation costs and import or carbon taxes.
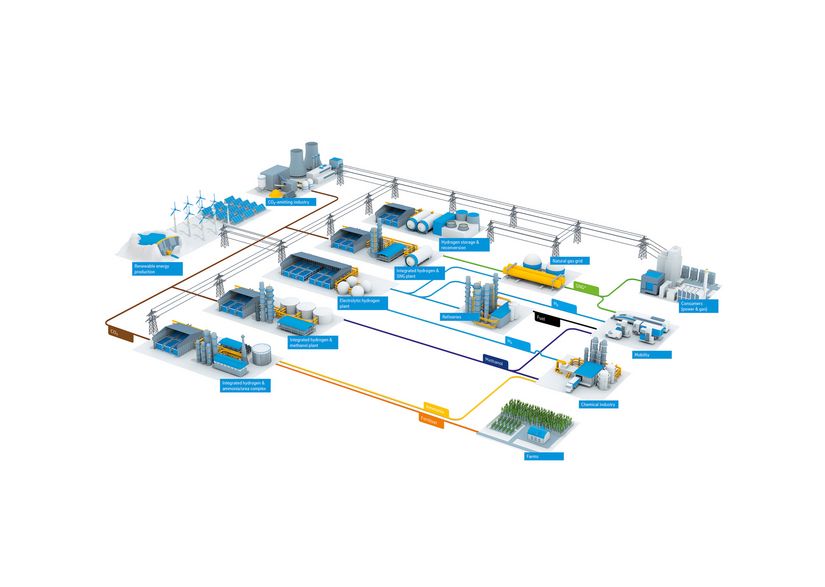
With decades of expertise in ammonia process technology and alkaline water electrolysis (AWE), a technology that enables a wide variety of environment-friendly production processes, thyssenkrupp decided to invest this know-how in developing a technically and economically feasible concept for small-scale, distributed ammonia production from renewable feedstocks. Whereas in conventional ammonia plants, hydrogen is produced by steam reforming natural gas, thyssenkrupp’s green ammonia concept uses AWE, while the nitrogen required for ammonia synthesis is produced by an air separation unit (ASU). AWE is based on the proven chlor-alkali electrolysis technology developed by thyssenkrupp Uhde Chlorine Engineers with their technology and EP(C) execution experience gained from more than 600 plants with over 10 GW capacity installed worldwide. All you need for green AWE-based hydrogen production is power from renewable sources and water. Moreover, AWE is ideally suitable for use in green ammonia plants as it can be started up within minutes and follows load variations within seconds.
thyssenkrupp has developed two production concepts: a 50 mtpd plant based on 20 MW power input and 100% availability and a 300 mtpd production facility based on 120 MW power input. As the latter is approaching industrial scale, it could be an interesting revamping option for greening existing plants. This reduces engineering and construction costs while facilitating implementation – a fast-track solution for potential customers.
Of course small-scale green ammonia plants can only be viable if they make economic sense, i.e. can compete under certain circumstances with conventional plants. thyssenkrupp evaluated the five key viability drivers – capital expenditure, availability and cost of renewable power, possible restrictions on and cost of ammonia transportation, CO2 emission restrictions, and CO2 taxes – and came to the conclusion that at landlocked locations with low power costs installation of a green ammonia plant may well be an interesting option, not least for the fertilizer or chemical industry. Not surprisingly, economies of scale favor conventional plants at higher production capacities. But besides its economically feasible existence as a niche product, green ammonia is becoming increasingly interesting to renewable energy producers as a suitable energy storage and carrier medium.